- Download Halliburton Energy Services Usb Devices Driver Download
- Download Halliburton Energy Services Usb Devices Driver Updater
- Download Halliburton Energy Services Usb Devices Driver Windows 7
The equipment includes an electronic triggering device (ETD) that enables safe detonation of explosive devices, a battery-operated, electro-mechanical tool that sets wellbore devices on slickline and braided line without explosives, an electronic measurement system that automatically corrects measurement inaccuracies resulting from line stretch. Get directions, reviews and information for Halliburton Energy Services, Inc. Halliburton Energy Services, Inc. 3000 N Sam Houston Pkwy E Houston TX 77032. Reviews (281) 575-3000 Website. Menu & Reservations Make Reservations. Order Online Tickets.
Purpose
This section describes USB emulated device (UDE) support in the Windows operating system, for developing an emulated Universal Serial Bus (USB) host controller driver and a connected virtual USB device. Both components are combined into a single KMDF driver that communicates with the Microsoft-provided USB device emulation class extension (UdeCx).
Development tools and Microsoft-provided binaries
The Windows Driver Kit (WDK) contains resources that are required for driver development, such as headers, libraries, tools, and samples.
To write a function controller driver, you need:
- UdeCx: (udecx.sys) a WDF extension used by the function driver. This extension is included in Windows.
- Link to the stub library (Udecxstub.lib). The stub library is in the WDK.
- Include Udecx.h provided in the WDK.
Version history
UDE version 1.0.
KMDF version 1.15.
UMDF is not supported.
This invention relates to a vibrating device for use in sand control and formation stimulation in an oil and gas recovery operation.
Many oil and gas downhole recovery operations, especially high-rate, high-permeability completions, produce reservoir fluids that contain fines, or formation sand. Therefore, support and screening devices, such as screens, slotted liners, and the like, have been utilized to support gravel packs, or the like, in the well to stabilize the formation while permitting the recovered fluids to pass from the formation into the wellbore while preventing passage of fines or formation sand with the recovered fluids.
These support devices are often placed in a pressure-drop zone that subjects the devices to contamination from scaling (salt crystal growth) and other materials that are precipitated during production of the reservoir fluids (hereinafter collectively referred to as “scale”). Thus, the scale must be removed from the devices either mechanically, which adds to the labor and cost of the project, or chemically, which may harm the metal parts of the devices. Also, during the recovery operation from the wellbore, a “skin” develops around the wall of the wellbore that impedes the flow of fluid from the formation thus requiring techniques to remove the skin.
Therefore, what is needed is a device of the above type that simultaneously performs the above screening as well as the scale and skin removal functions, yet eliminates the above problems.
FIG. 1 is a diagrammatic view of an embodiment of a sand control system of the present invention shown in a downhole environment.
FIG. 2 is a flow chart depicting steps of a method according to an alternate embodiment of the invention.
FIG. 3 is a graph depicting two variables in accordance with the embodiment of FIG. 2.
Referring to FIG. 1 of the drawings, the reference 10 refers, in general, to a wellbore 10 that penetrates a producing formation F. It is also understood that a casing (not shown) can be provided in the wellbore 10 and that production tubing (not shown) is installed in the wellbore 10.
Four axially-spaced, cylindrical gravel pack support and screening devices 12a–12d are mounted, in any conventional manner, to the wall of the wellbore 10 adjacent the formation F. The devices 12a–12d can be in the form of screens, slotted liners, or any similar type of gravel support device. Although not clear from the drawing due to scale limitations, it is understood that the devices 12a–12d define an annular space with the wall of the wellbore 10 that receives one or more gravel packs, or the like, (not shown). The purpose of each gravel pack is to improve the integrity of the wall of the wellbore 10, yet allow recovered fluids to pass to and through the devices 12a–12d and into the wellbore, while preventing the passage of fines or sand from the fluids. Since these gravel packs are conventional, they will not be described in any further detail.
Two electrical drivers 16a and 16b are mounted on the inner wall of the device 12b in a diametrically opposed relationship. The drivers 16a and 16b are conventional and, as such, are connected to a source of AC or DC power in a manner to be described and are adapted to supply electrical power, for reasons to be described.
A transducer 20a is mounted on the wall of the wellbore 10 between the devices 12a and 12b; a transducer 20b is mounted on the wall of the wellbore 10 between the devices 12b and 12c; and a transducer 20c is mounted on the wall of the wellbore 10 between the devices 12c and 12d. The transducers 20a–20c can be in the form of conventional electromechanical transducers, or converters, such as tuning forks, cantilevers, oval-mode tools, magnetostrictive drivers, or piezoelectric transducers. It is understood that each transducer 20a–20c is electrically connected to one of the drivers 16a or 16b so that it can be driven by the electrical power output from the driver to cause the transducer to vibrate accordingly.
The transducers 20a–20c are designed to operate at a desired, predetermined frequency, and preferably at their resonate frequency. For example, one or more of the transducers 20a–20c can be designed to operate at a relatively high resonate frequency; while the other transducer(s) can operate at a relatively low resonate frequency. As a non-limitative example, if the desired frequency is above 4 kHz, the transducers 20a and 20b can be in the form of piezoelectric transducers, such as those marketed under the designation PZT-4 by the Edo Corporation of Salt Lake City, Utah. In this case, the transducers 20a and 20b are connected to the driver 16a and the frequency, or frequencies, of the output of the driver 16a is matched to the resonate frequencies of the transducers 20a and 20b so that they are driven at their resonate frequencies. If it is desired to operate below 4 kHz, the transducers 20c and 20d can be in the form of conventional magnetostrictive drivers that are connected to the driver 16b, in which case the frequency, or frequencies, of the output of the driver 16b is matched to the resonate frequencies of the transducers 20c and 20d so that they are also driven at their resonate frequencies.
The transducers 20a–20c are mechanically coupled to the devices 12a–12d in a manner so that vibrations of the transducers 20a–20c are imparted to the devices 12a–12d. The coupling is such that the devices 12a and 12b provide equal and opposite loads on the transducer 20a, so that it can be used to vibrate the devices 12a and 12b simultaneously. Similarly, the devices 12b and 12c provide equal and opposite loads on the transducer 20b so that it can be used to vibrate the devices 12b and 12c simultaneously; and the devices 12c and 12d provide equal and opposite loads on the transducer 20c so that it can be used to vibrate the devices 12c and 12d simultaneously.
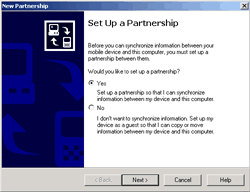
A sensor 22a is mounted to the outer surface of the device 12b and a sensor 22b is mounted between the outer surfaces of the devices 12c and 12d. Also, two axially spaced sensors 22c and 22d are mounted to the inner surfaces of the devices 12a and 12c, respectively. The sensors 22a and 22b are adapted to sense pertinent downhole data, such as pressure and temperature, outside the devices 12a–12d, and the sensors 22c and 22d are adapted to sense the same data inside the devices.
A control unit 24, which can include, or be in the form of, a microprocessor, or the like, is mounted to the upper end of the device 12a. Although not shown in the drawings in the interest of clarity, it is understood that the control unit 24 is electrically connected to the sensors 22a–22d so that the data sensed by the sensors 22a–22d is transferred to the control unit 24. The control unit 24 is adapted to process signals from the sensors 22a–22d and generate corresponding output signals. The drivers 16a and 16b are also connected to the control unit 24 so that the control unit 24 can provide a signal to the drivers 16a and 16b to enable them to drive the transducers 20a–20c.
A telemetry device 26 is mounted on the upper end of the control unit 24. The telemetry device 26 is electrically connected to the control unit 24 and, as such, is adapted to collect the data from the control unit 24 and transmit the data to the ground surface. Since the telemetry device 26 is conventional, it will not be described in detail.
It is understood that the devices 12a–12d, the drivers 16a and 16b, the transducers 20a–20c, the sensors 22a–22d, the control unit 24, and the telemetry device 26 can be assembled as a single unitary package before being inserted in the wellbore 10 in a conventional manner.
A cable assembly 28, shown by a dashed line, extends from the ground surface to the telemetry device 26 and to the control unit 24. It is understood that the cable assembly 28 includes electrical conductors for supplying electrical power from the ground surface. Although not shown in the drawings in the interest of clarity, it is also understood that the cable assembly 28 extends to drivers 16a and 16b and the sensors 22a–22d to also power these units.
In operation, the package consisting of the devices 12a–12d, the drivers 16a and 16b, the transducers 20a–20c, the sensors 22a–22d, the control unit 24 and the telemetry device 26 is inserted in, and mounted to, the wellbore 10 adjacent the formation F as shown in FIG. 1. The devices 12a–12d are packed with sand, or the like, to form gravel packs and production is started. Fluids recovered from the formation F pass through the gravel packs and the devices 12a–12d and upwardly in the wellbore 10 to the above-mentioned production tubing (not shown) for passing to the ground surface, while the devices 12a–12d prevent fines or sand from the fluids from passing with the fluids.
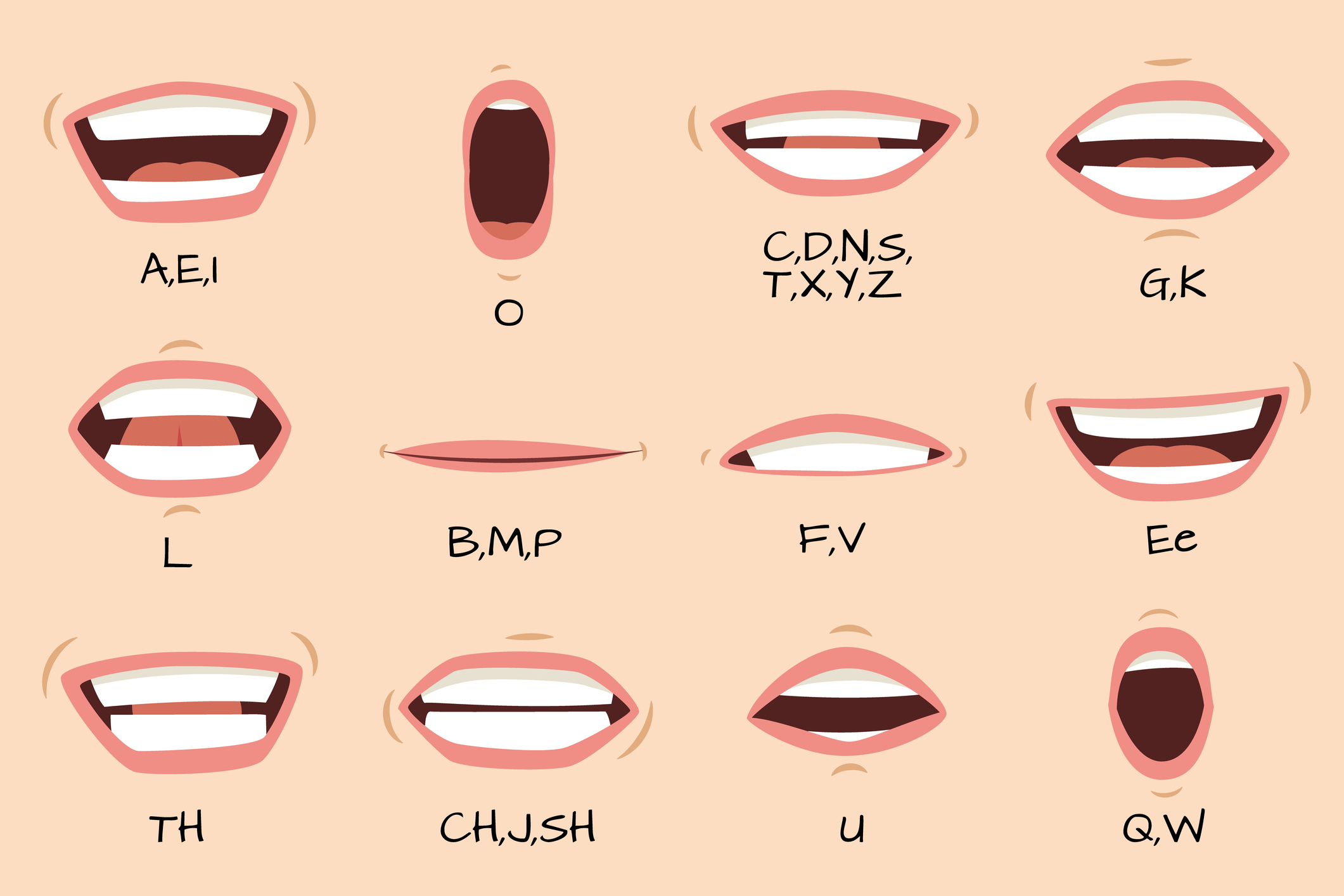
The sensors 22a and 22b sense the pertinent downhole data, such as pressure and temperature, outside the devices 12a–12d, and the sensors 22c and 22d sense this data inside the devices 12a–12d. Each sensor 22a–22d generates corresponding signals that are transmitted to the control unit 24. The control unit 24 processes and analyzes the above signals and is programmed to respond when the fluid pressure outside the devices 12a–12d exceeds the fluid pressure inside the devices 12a–12d by a predetermined amount, indicating that the devices 12a–12d are at least partially clogged with scale. When this happens, the control unit 24 sends a corresponding signal to the drivers 16a and 16b to activate them.

The power output from the drivers 16a and 16b drive their corresponding transducers 20a–20c to cause corresponding vibration of the transducers 20a–20c and therefore the devices 12a–12d at their resonate frequency in the manner discussed above. These vibrations fracture, or break up, the scale accumulating on the devices 12a–12d. The scale and/or materials recovered from the devices 12a–12d are allowed to fall to the bottom of the wellbore 10, or could be circulated, in any conventional manner, to the ground surface for recovery. In the meantime, the downhole data from the control unit 24 is transmitted to the telemetry device 26 which, in turn, transmits it to the ground surface for monitoring and/or processing.
The output from the transducers 20a–20c can be in a frequency range that also stimulates the formation F adjacent the devices 12a–12d and reduces the “skin” around the wellbore 10 that can slow the flow of production fluid from the formation to the wellbore.
As a result of all of the foregoing, scale accumulating on the devices 12a–12d is broken up without causing any physical or chemical damage to the devices 12a–12d, while the formation F is stimulated and the skin around the wellbore 10 is reduced.
The above operation can be terminated after a predetermined amount of time or after the control unit 24 ceases sending the above signal to the drivers 16a–16b in response to data received from the sensors 22a and 22b indicating sufficient scale has been removed from the devices 12a–12d.
According to another embodiment of the invention as shown in FIG. 2, the sensors 22a–22d are eliminated and a reservoir model can be utilized to provide information relating to the need to vibrate the devices 12a–12d in the above manner. Otherwise the embodiment of FIG. 2 contains the same components as the embodiment of FIG. 1. According to the embodiment of FIG. 2, data is initially collected to generate an initial reservoir model that is inputted to the control unit 24. After production of fluid from the formation F is initiated, the production information is generated and inputted to the control unit 24 which matches the information to the initial model and adjusts the model as necessary to set a working model. As production continues, the additional production data is collected and inputted to the control unit 24 which compares the data to the working model. If there is a match, the data is fed back to the control unit 24 for further processing; and, if there is no match, the drivers 16a and 16b are actuated to drive the transducers 20a–20c in the manner discussed above and thus initiate the vibration/production stimulation cycle described above.
FIG. 3 is a graph of the simulated production from the wellbore 10 vs. time and shows the reservoir model of FIG. 2 by the rectangular data points, and a deviation from the model by the triangular data points, both before and after the scale is removed from the devices 12a–12d and the formation F is stimulated, including removal of the skin, in accordance with the foregoing method which can bring the production back to the model values.
Thus, the system and method according to the above embodiments performs the screening and stimulation functions yet eliminates the problems discussed above. Moreover, the above sensing, analysis, and treatment can be done simultaneously in real time.
Download Halliburton Energy Services Usb Devices Driver Download
Several variations may be made in both of the above embodiments without departing from the scope of the invention. These variations are as follows:
1. The control unit 24 can be programmed to adjust the pressure differential required to actuate the drivers 16a and 16b.
2. The number, type, and location of the screening devices 12a–12d, the drivers 16a and 16b, the transducers 20a–20c, and/or the sensors 22a–22d can be varied.
3. The sensors 22a and 22b could be eliminated and a scale sensor, or detector, could be mounted on each device 12a–12d to directly detect the presence of scale, and any other foreign materials, and generate a corresponding output signal that is transmitted to the control unit 24 for processing in the above manner.
4. The control unit 24 can be in the form of any type of data processing device.
Download Halliburton Energy Services Usb Devices Driver Updater

5. The above connections between the control unit 24, the drivers 16a and 16b, and the sensors 22a–22d, the connections between the drivers 16a and 16b and the transducers 20a–20c, and the connection between the telemetry device 26 and the ground surface could be wireless.
6. The cable assembly 28 could be eliminated and a battery pack, or the like, could be provided downhole to supply electrical power to the various units.
Download Halliburton Energy Services Usb Devices Driver Windows 7
7. Rather than use the reservoir model discussed in connection with FIG. 2 instead of the sensors 22a and 22b, the reservoir model could be used in addition to the sensors 22a–22b.
The foregoing descriptions of specific embodiments of the present invention have been presented for purposes of illustration and description. They are not intended to be exhaustive or to limit the invention to the precise forms disclosed, and obviously many modifications and variations are possible in light of the above teaching. The embodiments were chosen and described in order to best explain the principles of the invention and its practical application, to thereby enable others skilled in the art to best utilize the invention and various embodiments with various modifications as are suited to the particular use contemplated. It is intended that the scope of the invention be defined by the claims appended hereto and their equivalents.
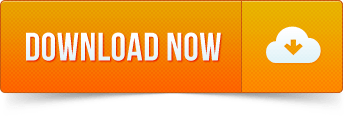